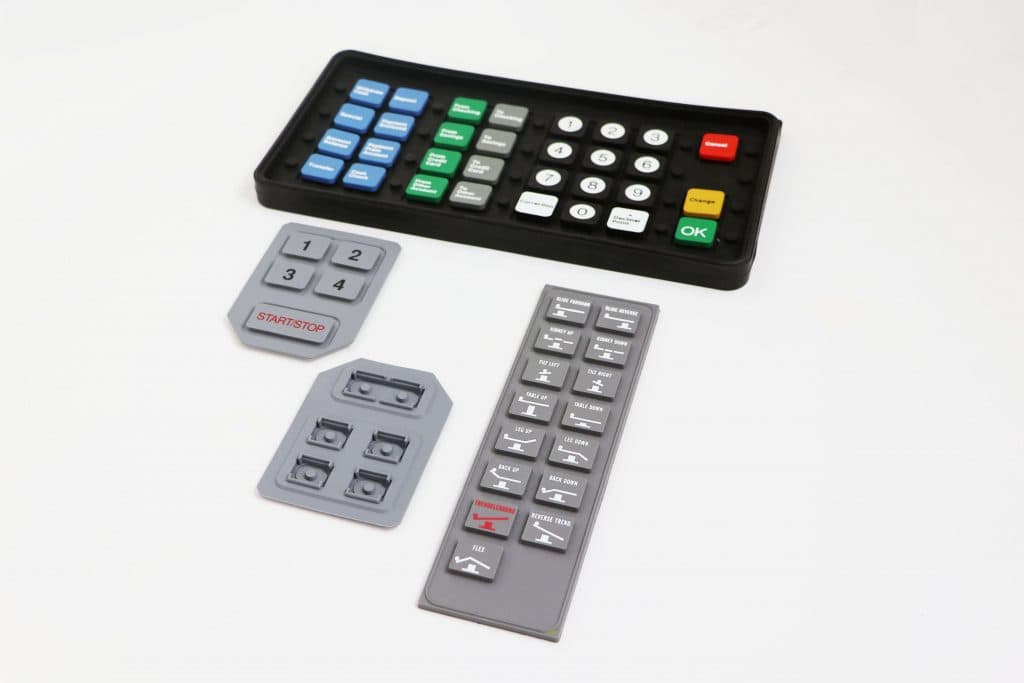
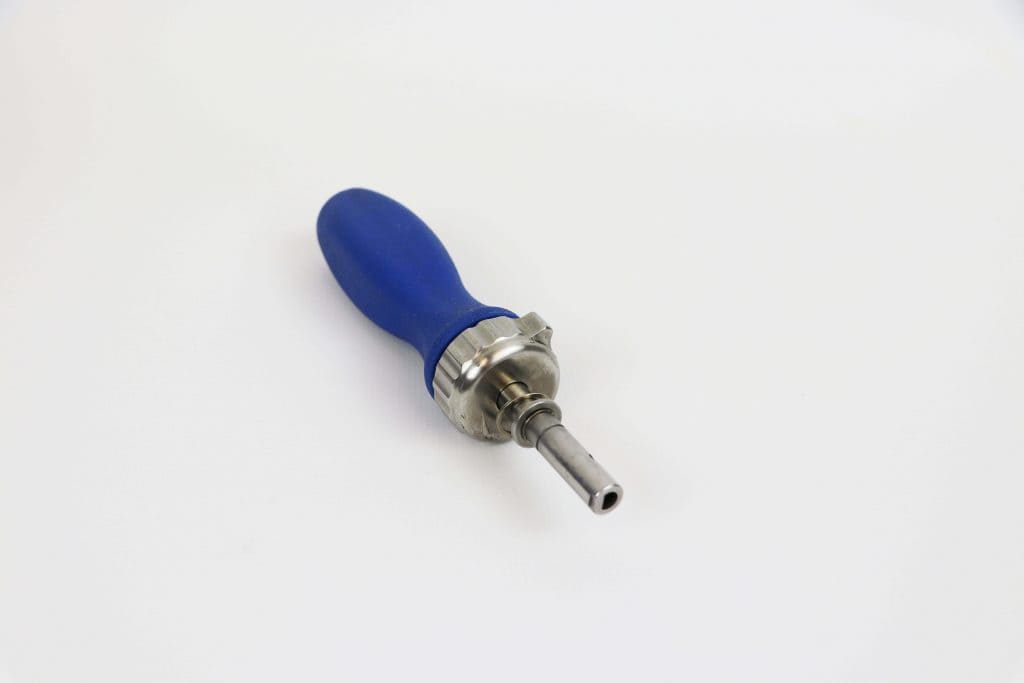
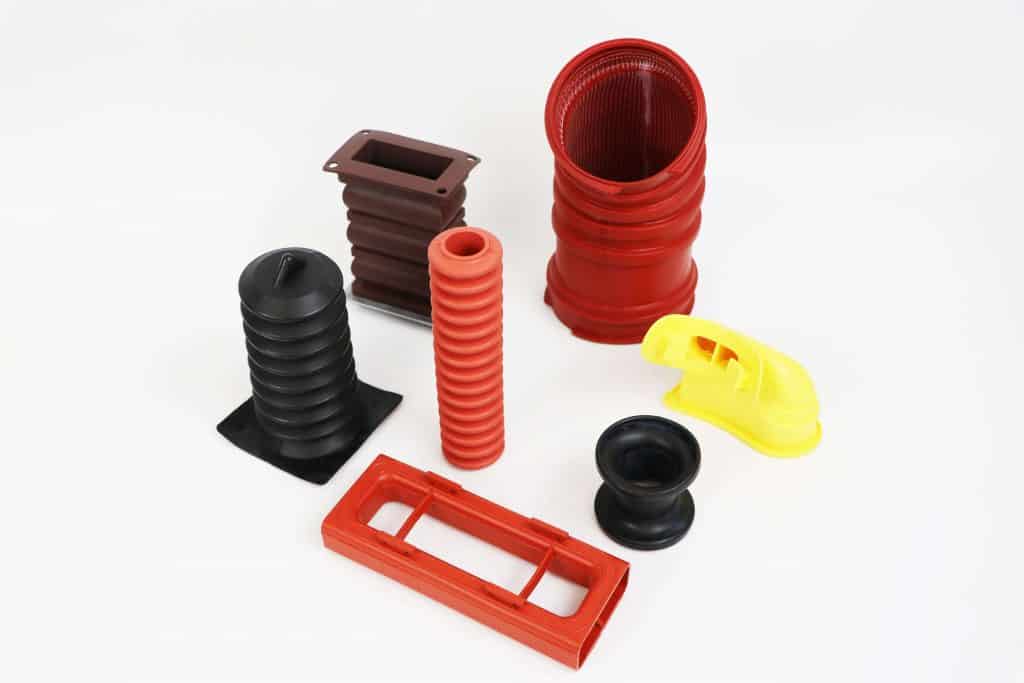
MOLDED SILICONE PRODUCTS
ARCO Silicone is a fourth-generation, family-owned company with more than 175 dedicated team members. Our silicone products are Made in America, ensuring better service, faster shipping, higher fill rates, and consistent quality. We continue to innovate and push the boundaries in creating custom silicone extrusions and custom-molded silicone parts.
Our talented and experienced engineers work closely with our customers to design and produce molded silicone parts to their exact specifications. This page will discuss some of the most common silicone molding methods to inform the sourcing process.
OUR SILICONE MANUFACTURING PROCESSES AVAILABLE
Numerous silicone molding processes are available, each featuring different advantages for various applications. Understanding the differences between available molding processes is essential to selecting the best method for a specific design.
ARCO Silicone offers the following processes for custom-molded silicone products:
- Liquid Silicone Rubber (LSR) Injection Molding. This fabrication method uses a mechanical mixing process to combine the two-component silicone compound before it is heat-cured in the mold. Liquid silicone has exceptional heat- and flame-resistant qualities and high formability. LSR creates injection-molded silicone products with superior durability, tensile strength, flexibility, and accuracy, making them ideal for automation and 24/7 production.
- Compression Molding. Compression molding is well-suited to the production of simple parts requiring only medium precision. The process starts with placing an uncured disk of rubber into a heated, pressurized form where it stays until it finishes curing. Compression molding produces electrical components, HVAC parts, fuel system components, automotive parts, hydraulic and pneumatic seals, and sterile tubing for food and beverage equipment. The advantages of compression molding include low cost, short lead times, easy prototyping, and the broadest range of part sizes.
- Injection Compression Molding (ICM). ICM is a hybrid of LSR and compression molding. It starts with injecting the melted silicone into a partially opened mold. As the mold closes, the compression forces the silicone into the rest of the mold cavity. This silicone manufacturing method is well-suited to producing large volumes of lightweight and robust silicone products, such as gears.
- Transfer Molding. Transfer molding uses a plunger to force silicone into the mold. This method uses a high-consistency rubber that is too thick for injectors. Transfer molding is common for creating parts with embedded components like prongs, semiconductor chips, or ceramics.
- Overmolding. Overmolding adds a silicone layer to a completed part, such as adding silicone grips to molded tools. It takes careful planning to produce a quality over-molded product, as the materials must be compatible to ensure adhesion between layers.
AVAILABLE MATERIALS
While silicone is a versatile material option, other elastic polymers may sometimes be better suited to the design. The materials available at ARCO Silicone include, but are not limited to:
- Chloroprene
- EPDM (Ethylene Propylene Diene Monomer)
- Ethylene acrylate
- Fluorocarbon
- Fluorosilicone
- Foam silicone
- HNBR
- Natural rubber
- Nitrile
- Polyacrylate
- SBR/Nat
- Silicone
- TPE (Thermoplastic Elastomers)
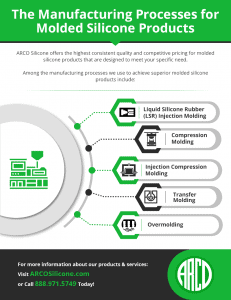
SUPERIOR CUSTOM-MOLDED SILICONE PRODUCTS
ARCO Silicone has been a leader in silicone manufacturing for almost a century. Our team offers extensive experience with a broad range of elastomers, including silicone. That gives us a wide range of options to meet every specification for your part’s performance, quantity, size, and cost.
To learn more about our capabilities, please view our brochures. To see how we can help with your project, please contact us or request a quote
Molded Silicone Parts
Can be produced in various shapes and sizes, cut to order, and packaged in bulk.